相信各位对于蔚来汽车,很多人应该都已经不陌生了,蔚来造的第一款量产车是一款动力达1360匹马力的电动超跑——EP9,它于2016年下线,并在全球多个赛道创造了圈速记录,顿时让蔚来名声大噪。随后在2017年,高性能智能电动7座SUV——ES8,12月正式上市,补贴前指导价区间为44.80-54.80万元,首批10000台创始版车型被预定一空。那么小编好奇,这么一款高品质的电动SUV是如何制造出来的?在2018年10月24日,我们带着满满的期待和疑问,走进合肥先进制造基地,揭开关于蔚来更多的秘密。
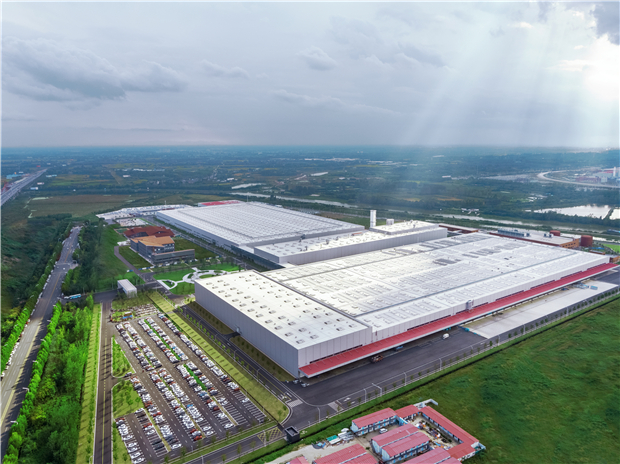
探秘合肥先进制造基地
这次 NIO House 的选址可谓是一次大胆的尝试,把一家蔚来中心和ES8的制造基地共同放在一起。蔚来的创始人、董事长兼CEO李斌先生表示:其实这个NIO House算整个工厂的前厅,可以对用户、媒体、各个合作伙伴开放工厂的参观。据悉,蔚来合肥先进制造基地由蔚来与江淮联合打造,但蔚来品牌不会与江淮品牌共线生产。它位于合肥市经济技术开发区,占地约839.6亩,总建筑面积约23万平方米。这座全新智能高端电动车制造基地按照业内最高标准建设, 设有冲压、车身、涂装以及总装四大工艺车间,拥有国内最新全铝车身生产线,另外还建有质量中心、试车跑道、能源中心、蔚来中心和综合办公区。
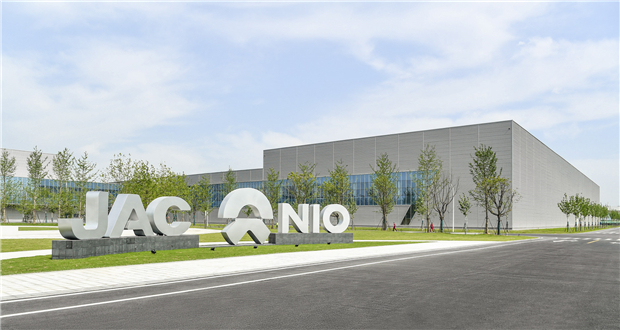
蔚来表示,发展电动汽车是中国汽车产业升级的重要核心,而企业间优势互补、共赢发展,是我国新能源汽车产业构筑全球竞争力的必由之路。蔚来汽车拥有前瞻的理念和雄厚的技术资源, 江淮汽车在生产制造、供应链体系等方面具备深厚的积累和底蕴。两家公司强强携手,优势互补,高效整合资源,将快速提升我国新能源汽车产业的国际竞争力。
产能进展
全新制造基地采用订单生产制,年产能规划10万台智能纯电动汽车(双班),并具备可扩展性。截至2018年9月30日,蔚来已累计交付3,368台高性能电动7座SUV ES8,其中2018年第三季度交付量为3,268台。2018年9月单月交付量为1,766 台,较前月增长约58%。此外,通过生产线的持续改造升级,不仅能够满足不断增长的ES8订单需求,也将为预计于2019年6、7月交付的5座高端电动SUV ES6预留产能。
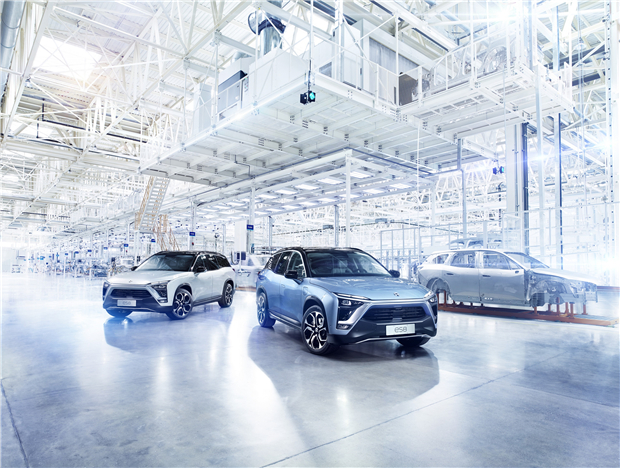
冲压车间
车间占地面积12672平方米。一条高精度、高柔性的无尘化冲压生产线,拥有2500吨伺服机械压力,其拉伸系统采用全球顶尖液压数控垫,更利于零件成型;搭配ABB直线七轴机器人,实现无人化生产。
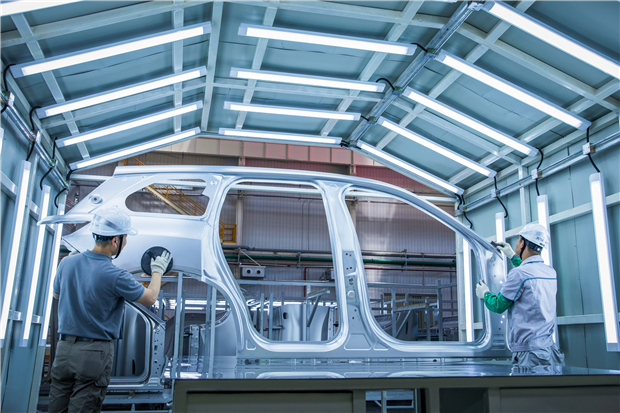
冲压车间生产21个冲压件生产,其中大型覆盖件模具来自日本富士,包括侧围、顶盖、电机盖等,天汽模则主要是门 板等。蔚来ES8拥有全球最大的铝侧围外板,拉伸深度高达380mm,代表了全球领先的铝材冲压产出水平。
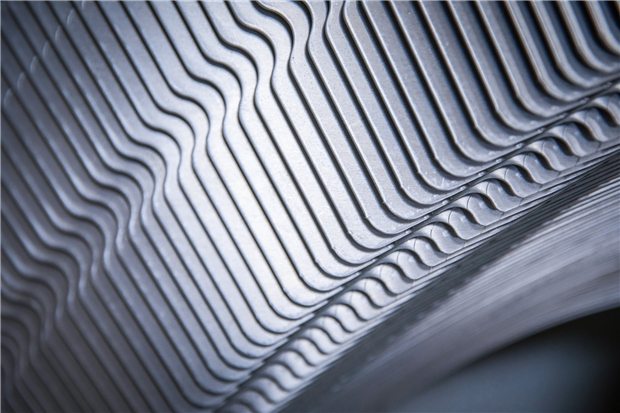
ES8的冲压工艺通过十多次的CAE模拟和回弹补偿,保证了冲压件的成型裕度,并通过长达10轮的模具调试优化,最终冲压件的精度达到了豪华车的水平:匹配部位+/-0.5mm。
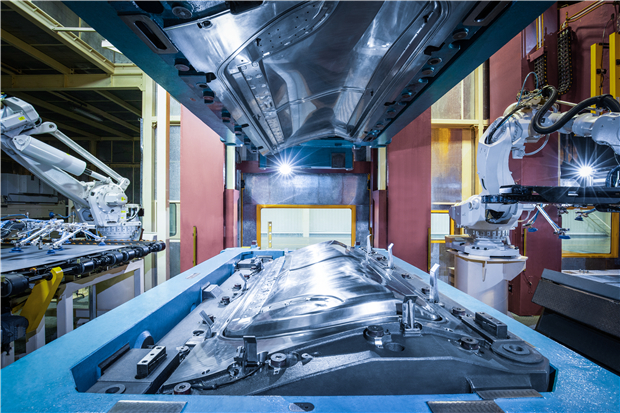
冲压线生产的每个零件都经过线尾检验人员的100%全方位检查,每批次都会进行表面质量抽检,用高亮油来模拟油漆后的状态;尺寸质量每批次进行3件关键点测量,确保零件的精度和稳定性。
国内最新的全铝车身生产线
没有粉尘、碎屑、烟雾,国内最新的全铝车身生产线占地面积为64800m²,相当于9个标准足球场大小。这里生产的首款车型为七座高性能智能电动SUV ES8,标准生产节拍15JPH(240秒/台),目前已扩展至20JPH(180秒/台)。ES8 的铝材使用率高达96.4%,全球量产车中最高。
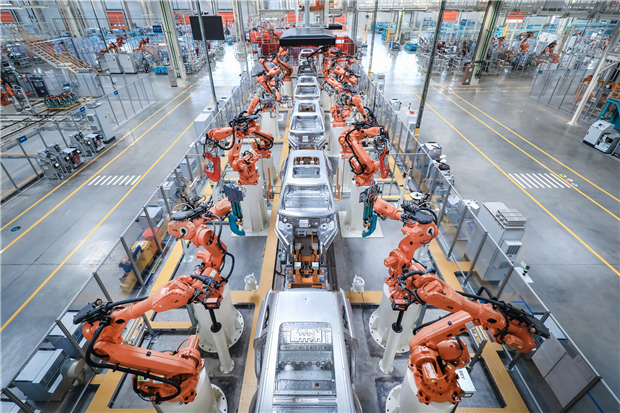
传统的钢结构车身主要采用焊接,不仅火花四溅,还伴随浓重的粉尘和焦糊气味。走进蔚来全铝车身车间,最直观的感觉是安静、干净,因为全铝连接主要采用铆接技术,温度适宜,噪音小,同时车间在部分连接工位设有除尘装置,会对点焊区、弧焊区、激光焊区,焊接过程中产生的微量烟尘, 进行吸风换风处理,整个车间符合当下减排和环保要求。
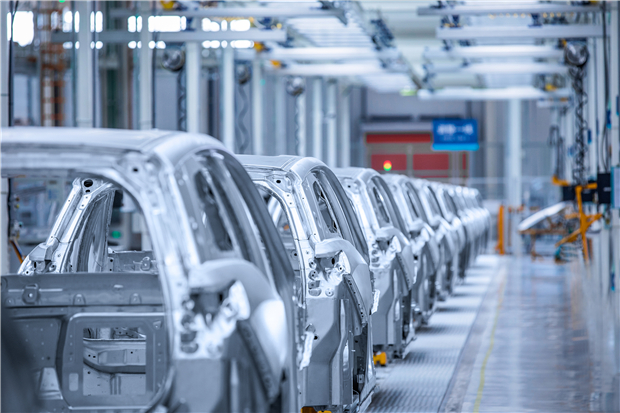
最新设备,核心工位100%自动化
由江淮和蔚来按照最新的技术体系和产线标准建设,由全球顶尖的合作伙伴⸺瑞典ABB、法国ARO、德国DEPRAG、 史丹利百得集团等合力打造。307台机器人实现车身主要连接100%自动化,车间整体自动化率97.5%,是国内最现代化的全铝生产线。
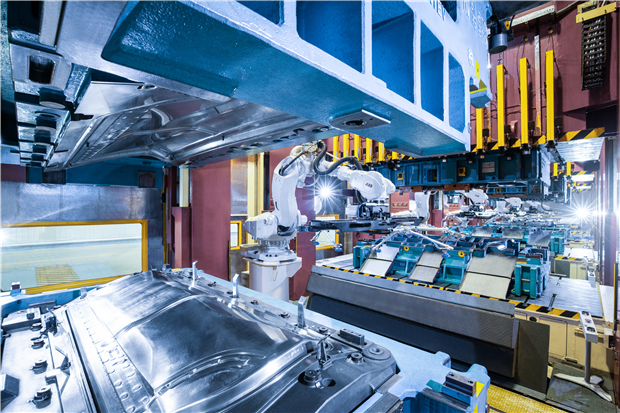
全球产量的全铝车身中最高比例的铝材应用量-96.4%
ES8铝材的使用率高达96.4%,这也是全球量产的全铝车身 中最高比例的铝材应用量。(高于捷豹XFL的75%,凯迪拉克CT6的58%)
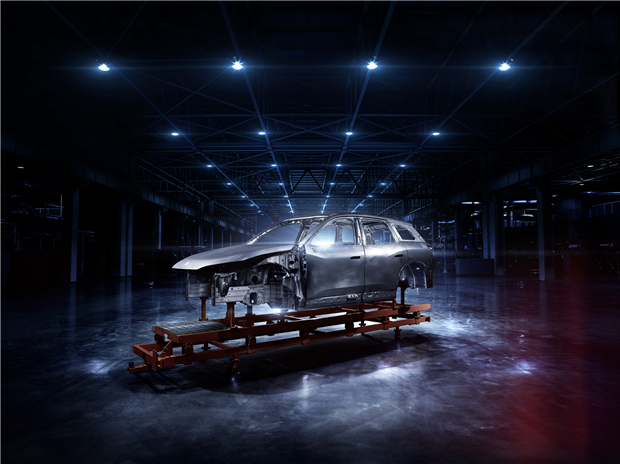
在正确的地方使用正确的材料
为了确保整车强度,ES8白车身综合使用了3系、5系、6系和7系铝材。其中,3系合金为真空高压压铸铝合金,具有强度高、尺寸精度高的特点, 能成形复杂结构,促进设计轻量化;板材方面5系分布比较分散,主要用于四门一盖和支架;6系板材主要分布在车顶、地板和前舱等处,保证乘员安全;挤压铝合金(挤压型材)主要是6系和7系,7系挤压材料特别选用7003号变形铝材。ES8在 主前后纵梁、前保吸能盒等部位应用了7003号铝材,共6个件。其中前纵梁部的应用件最大,两侧共计10.4kg。7003号铝材强度高,具有优异的冲击韧性和吸能表现,多用于军事器材、装甲板和导弹装置。
航空级全铝连接工艺 最复杂的工位有16个ABB机器人组成
ES8全铝车身轻量化材料的应用在实现车身减重的同时,也对相应连接技术提出了更高的要求。其最大的挑战不仅在于需斥巨资建造先进生产线、更高昂的铝材成本,还需要通过采用多种连接工艺互补,实现最精益求精的生产工艺。
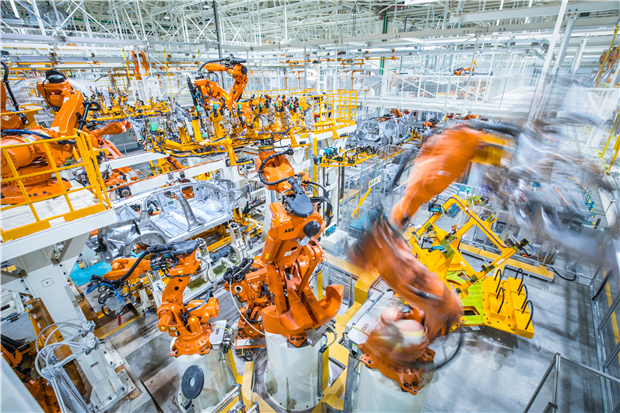
外总拼工位,共计有16台ABB机器人,是目前车身车间工艺操作最复杂的工位,它由4个上件机器人、8个SPR铆接机器人、2个FDS机器人及2个铝点焊机器人通过PLC程序控制同时作业。
大数据实时监控每一台车身数据
机器人通过德国进口巴斯勒(Basler)工业探头,精密监控167 个车身关键尺寸,自动采集测量数据,并通过计算机进行统计、分析、存储数据和信息,得出判定结果,即使在光环境较为复杂的车间中也可以进行精确的扫描,极大限度避免和减少不合格产品的产生。
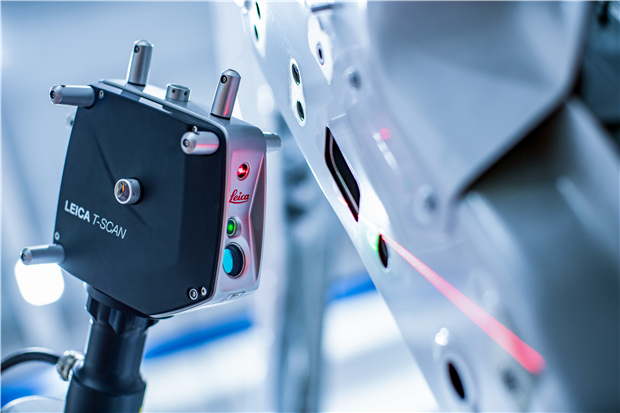
此外,专用的白车身剖解实验室会对七项连接工艺进行剖解,并通过金相分析确认连接质量是否满足标准。
定期抽检,对每台白车身的1016个车身扫描点对比检测。
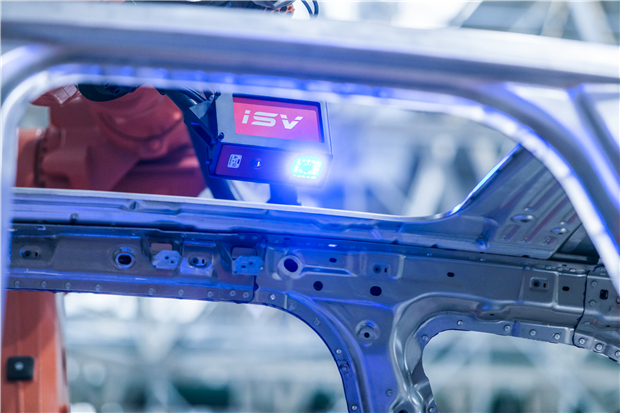
车身车间围绕全铝车身的最新连接工艺,充分考虑后期更多车型的兼容性及柔性化切换能力,可满足三款车型的共线生产要求。
43台机器人实现内外全自动车身喷涂
车间占地面积20724平方米,拥有43台全自动机器人,35台自动喷涂机器人+6台涂胶机器人UBS/UBC+2台涂胶机器人LASD。生产流程先进环保,保障制造的高品质。前处理采用 硅烷绿色前处理工艺,不含有害重金属,减少废液废渣排放。
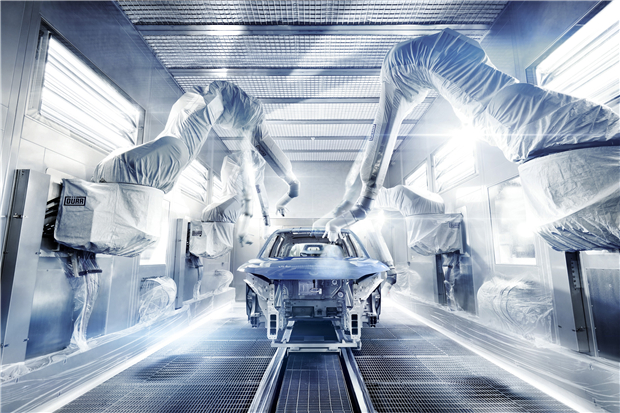
在车身颜色设计阶段就开始与全球最大的涂料供应商之一的德国巴斯夫涂料部(BASF Coatings)深度合作,无论是漆膜外观还是物理性能,度身定制的色彩配方和涂料工艺都达到了豪华车中的顶级水平。针对ES8采用订单化生产的特性,会通过FAS排队区域将同色订单优化排列,减少色漆喷涂中换色带来的浪费。
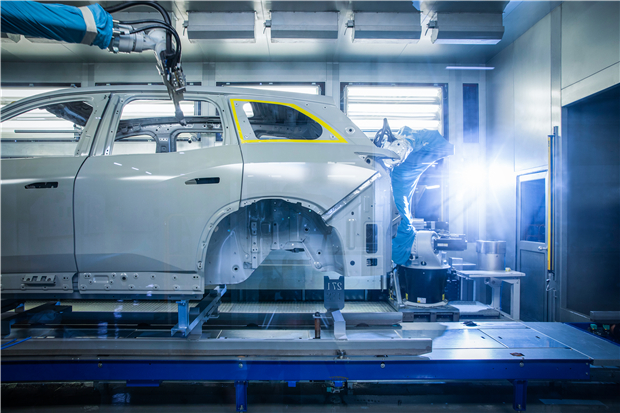
国内首个配备光新通道的涂装车间
车身有水平面,有垂直面,不同的光照上去,反射的角度不一样。曲面光源能保证光照角度的一致性,辅以可调节的色温,有利于精确检查油漆的缺陷。
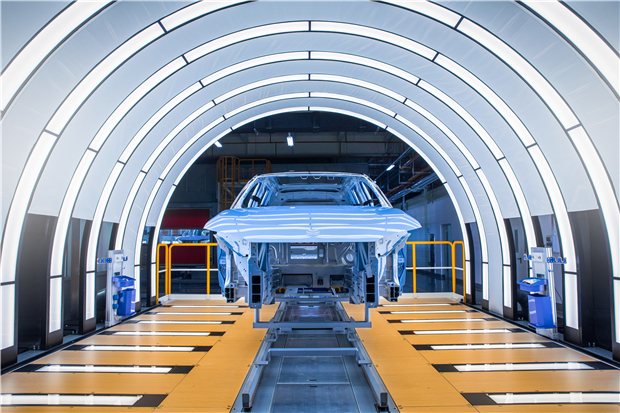
大数高据效+整互车联装+配智能
作为汽车制造四大工艺的最后一道流程,总装车间不但要负责整车装配、检测,更要做到可靠的品质保障。数字集约化管理,运用多层级设备进行智能化监控,能够提高生产效率,实现关键零部件在线防错。
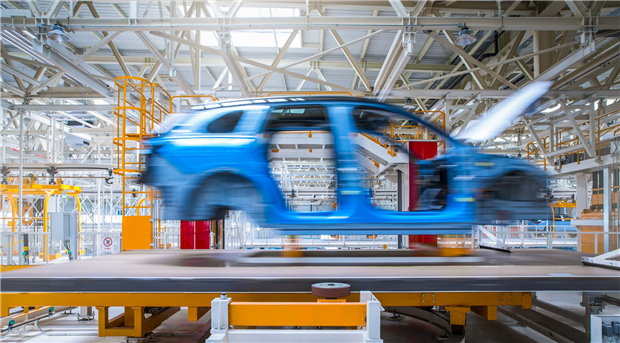
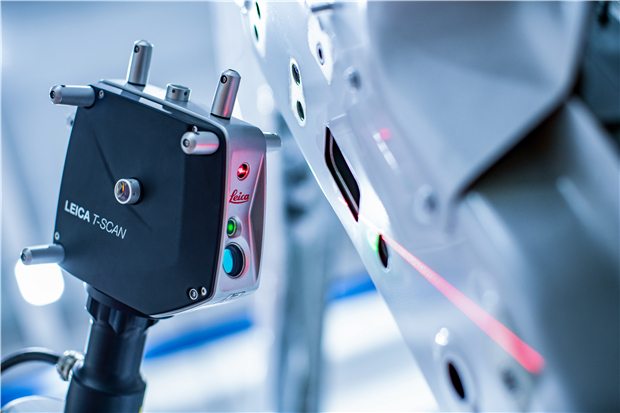
通过地源热泵技术实现厂房内温度调节的绿色工厂总装屋顶共有512个大小为16.2m²的全自动透明通风天窗, 可最大限度地使用自然光进行厂房内的照明。同时屋顶也布置有光伏发电板,最大程度地使用绿色能源,可使总装车间的总能耗下降20%。
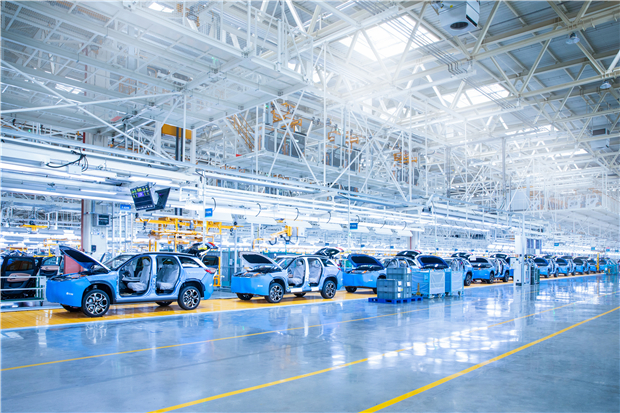
另外,总装车间使用地源热泵技术实现厂房内的温度调节, 一共安装了116个独立式空调模组,通过使用地下120米的深层水来进行热量交换,使厂房内的体感温度始终处于比较舒适的恒温状态。
整车装备过程实时监控,可追溯
作为以太网智能先进制造基地的核心之一,所有的电动工具已经全部装配了传感器,能够根据程序设计进行智能引导和防错,每一把电枪可以精确自动采集扭矩大小、扭矩曲线、转速、打紧顺序及角度,并通过QCOS系统进行拧紧指示和控制,当出现异常时系统会自动报警并与生产线体联动而自动停线,以确保扭力100%合格,确保整车品质。
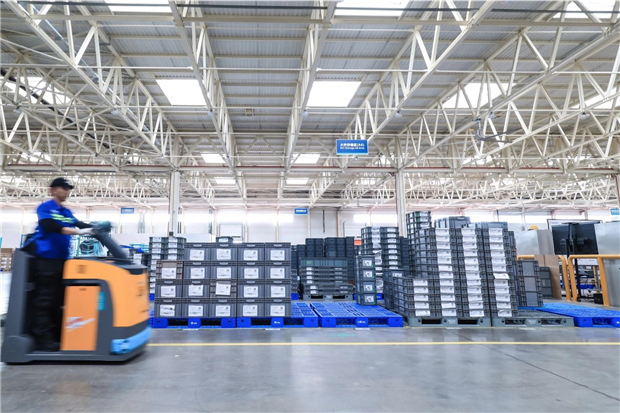
即使面对柔性化生产,同样从容实现多车型复杂程序智能拧紧。此外,所有的生产信息将汇聚成为大数据,进一步提升智能化水平。
全面的品控管理和质量检查
每一辆车从上线到下线交付,经过四大工艺和30多个检查工序、共计3000多项检查内容。这些检查和检查方法源于“过程质量管理”的理念,也包含了采集用户反馈后所作的深度调整。
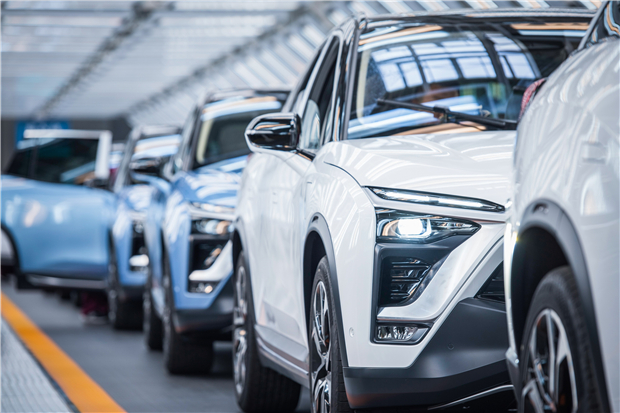
从四轮激光定位测量到高精度快速加液设备、便携式智能刷新,再到诊断设备等,均采用最新科技,每一个细节都通过精确的数据控制确保高品质。
结语:此次参观让我们对蔚来产品的诞生以及它充满高科技的制作流程有了初步的了解,了解了蔚来汽车是如何让精益生产更加精益求精。蔚来汽车虽然是个年轻的品牌,但拥有如此高科技、高品质、高服务的支撑,蔚来车型能够如此优秀确实是必然的,它宣示了中国在电动汽车方面的强大实力,以及互联网造车模式的潜力。